Custom plastic extrusion designed to your industry needs
Custom plastic extrusion designed to your industry needs
Blog Article
Key Benefits and Considerations of Applying Plastic Extrusion in Your Tasks

Comprehending the Basics of Plastic Extrusion
Plastic extrusion, a staple in the manufacturing sector, is a procedure that includes melting raw plastic material and reshaping it into a constant account. This profile, as soon as cooled down, can be cut right into desired lengths or curled for later use. The elegance of plastic extrusion hinges on its adaptability. A vast array of items, from piping to window frames, can be produced. The process needs an extruder, a detailed machine with a heated barrel, a rotating screw, and a die at the end. The plastic product, in the form of pellets, is fed right into the extruder, where it's melted and required via the die, taking its form. The choice of plastic and the layout of the die figure out the item's qualities.

The Economic Benefit of Plastic Extrusion
The economic advantage of plastic extrusion exists primarily in 2 locations: affordable product production and beneficial production speeds. With plastic extrusion, organizations can create high quantities of product at a reduced cost contrasted to other techniques. Moreover, the process boasts an impressive manufacturing rate, dramatically minimizing time and additional boosting its financial feasibility.
Economical Material Production
A substantial advantage of plastic extrusion is its impressive cost-effectiveness. This manufacturing process allows for continual, high-volume manufacturing with minimal waste, which equates right into lower costs. The raw products used, usually plastic pellets, are fairly economical compared to various other substances (plastic extrusion). The process itself calls for less power than many various other production approaches, even more reducing expenses. Additionally, the extrusion process allows for a high degree of precision in shaping the plastic, lowering the demand for costly post-production alterations or modifications. The toughness and durability of extruded plastic products commonly suggest much less need for substitutes, contributing to long-term savings. All these elements make plastic extrusion a very affordable choice for several tasks, offering an eye-catching balance in between price and efficiency.
Beneficial Manufacturing Speeds
While preserving the cost-effectiveness of the materials, an additional significant advantage of plastic extrusion hinges on its quick production rates. This performance in the manufacturing process is connected to the continual nature of the extrusion process, permitting high-volume production in a relatively short time period. The speed of manufacturing straight associates to a reduction in labor prices and a rise in outcome, therefore improving the general economic stability of the process. In addition, the busy production does not jeopardize the quality of the end product, making certain constant and reliable outcomes. This mix of quality, rate, and cost-effectiveness emphasizes the substantial economic advantage of carrying out plastic extrusion in various jobs.
Versatility and Personalization: The Staminas of Plastic Extrusion
Among the popular staminas of plastic extrusion hinges on its versatility and modification possibility. These top qualities open up the door to unrestricted design possibilities, giving manufacturers the capacity to tailor items to details requirements. This heightened level of personalization not just boosts item performance but likewise considerably boosts product uniqueness.
Unrestricted Design Opportunities
Plastic extrusion radiates in its capability to offer nearly limitless design possibilities. This technique gives flexibility to produce complicated shapes and elaborate profiles, a feat tough to accomplish with various other construction strategies. Owing to the liquid nature of molten plastic, the procedure is versatile sufficient to generate a varied range of dimensions, measurements, read what he said and types. The plastic can website link be adjusted to match one-of-a-kind requirements, enabling the manufacturing of personalized geometries and meeting certain client needs. Plastic extrusion can handle a variety of plastic kinds, expanding its application range. This versatile technique, as a result, offers a broad array of sectors from construction to automobile, product packaging to electronic devices, and beyond. With plastic extrusion, the design possibilities are basically countless.
Enhancing Product Individuality
The versatility of plastic extrusion can greatly boost item individuality. This process enables developers to trying out various forms, sizes, and colors, offering them the freedom to produce distinct products that stand apart on the market. It is this customization that provides a distinct identification per item, differentiating it from its rivals.
Along with its visual advantages, the customizability of plastic extrusion additionally offers useful advantages. Developers can change the homes of the plastic according to the certain demands of the application, boosting the item's performance. As an example, they can make the plastic much more adaptable, more durable, or more immune to warmth, relying on what the product requires. Hence, plastic extrusion not only boosts item uniqueness yet likewise its energy and bankability.
Layout Limitations in Plastic Extrusion: What You Need to Know
Exactly how can design constraints potentially influence the procedure of plastic extrusion? While plastic extrusion is versatile, style constraints can stop its benefits. Understanding these restrictions is vital for efficient implementation of plastic extrusion in your tasks.
Evaluating the Ecological Influence of Plastic Extrusion
While comprehending layout restrictions is a significant facet of plastic extrusion, it is similarly crucial to consider its environmental implications. The process visite site of plastic extrusion involves melting plastic materials, possibly releasing hazardous gases into the environment. Additionally, the resulting products are often non-biodegradable, adding to land fill waste. Nonetheless, innovations in technology have permitted even more environmentally-friendly techniques. Using recycled plastic materials in the extrusion process can lower ecological impact. Furthermore, developing eco-friendly plastic alternatives can help reduce waste problems. Examining these ecological aspects is crucial when carrying out plastic extrusion jobs, guaranteeing a balance in between efficiency, cost-effectiveness, and environmental responsibility.
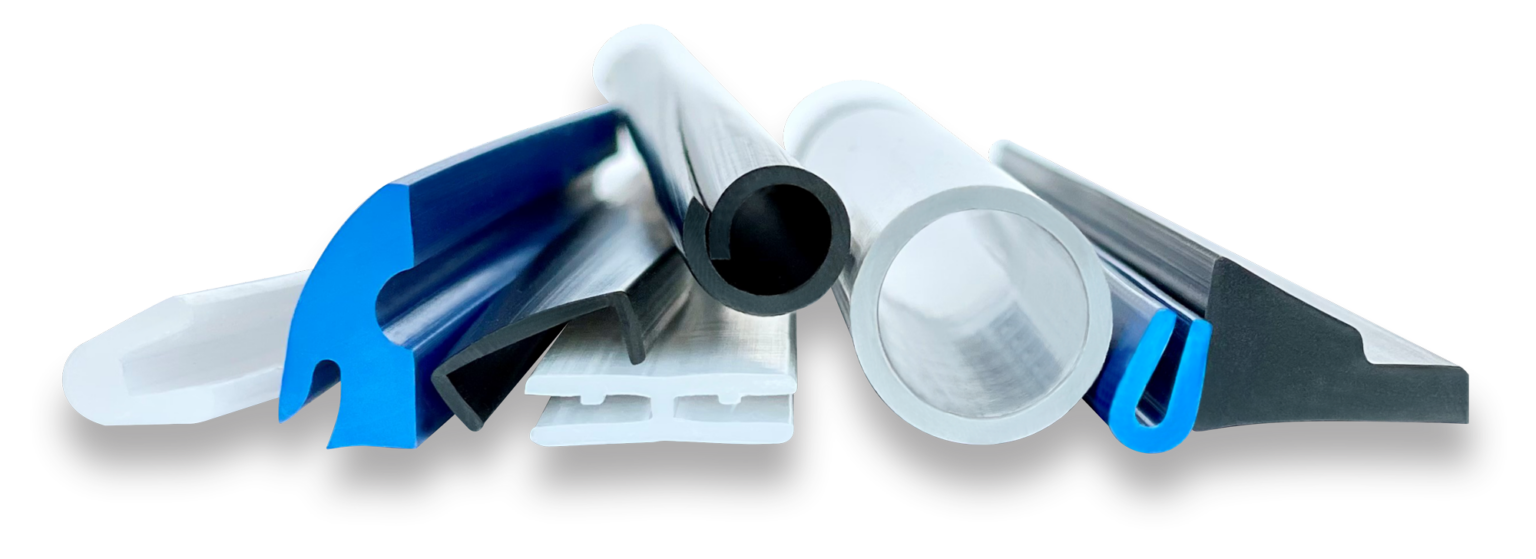
Study: Effective Projects Utilizing Plastic Extrusion
Success tales in the area of plastic extrusion are plentiful, demonstrating both the adaptability and performance of this manufacturing procedure. plastic extrusion. Another successful case is the production of plastic film for product packaging and farming. These circumstances show plastic extrusion's vital role in various fields, confirming to its versatility, cost-effectiveness, and reputable result.
Verdict
In conclusion, plastic extrusion supplies a effective and cost-effective method for creating complicated forms with minimal waste. Incorporating plastic extrusion into tasks can lead to effective end results, as confirmed by countless instance research studies.
Plastic extrusion, a staple in the manufacturing market, is a process that involves melting raw plastic product and improving it into a continual account. Plastic extrusion can handle a range of plastic types, expanding its application range.How can design limitations possibly impact the process of plastic extrusion? The process of plastic extrusion involves melting plastic materials, possibly releasing damaging gases into the setting. Utilizing recycled plastic products in the extrusion process can reduce environmental influence.
Report this page